Thermal digital twin for power electronics
What is a thermal digital twin?
Thermal digital twins are simulation models running in parallel of a physical system, with its parameters dynamically updated through lifetime based on real-time measurements. This ensures optimal accuracy in replicating the behaviour of the physical counterpart.
In the context of power electronics, thermal digital twins model the thermal behaviour of the power converter to estimate its temperature and overall state of health. By measuring a limited number of temperatures at selected points within a power module, a comprehensive equivalent thermal model is established. This model is then used to accurately estimate transistors’ temperatures and assess their level of degradation.
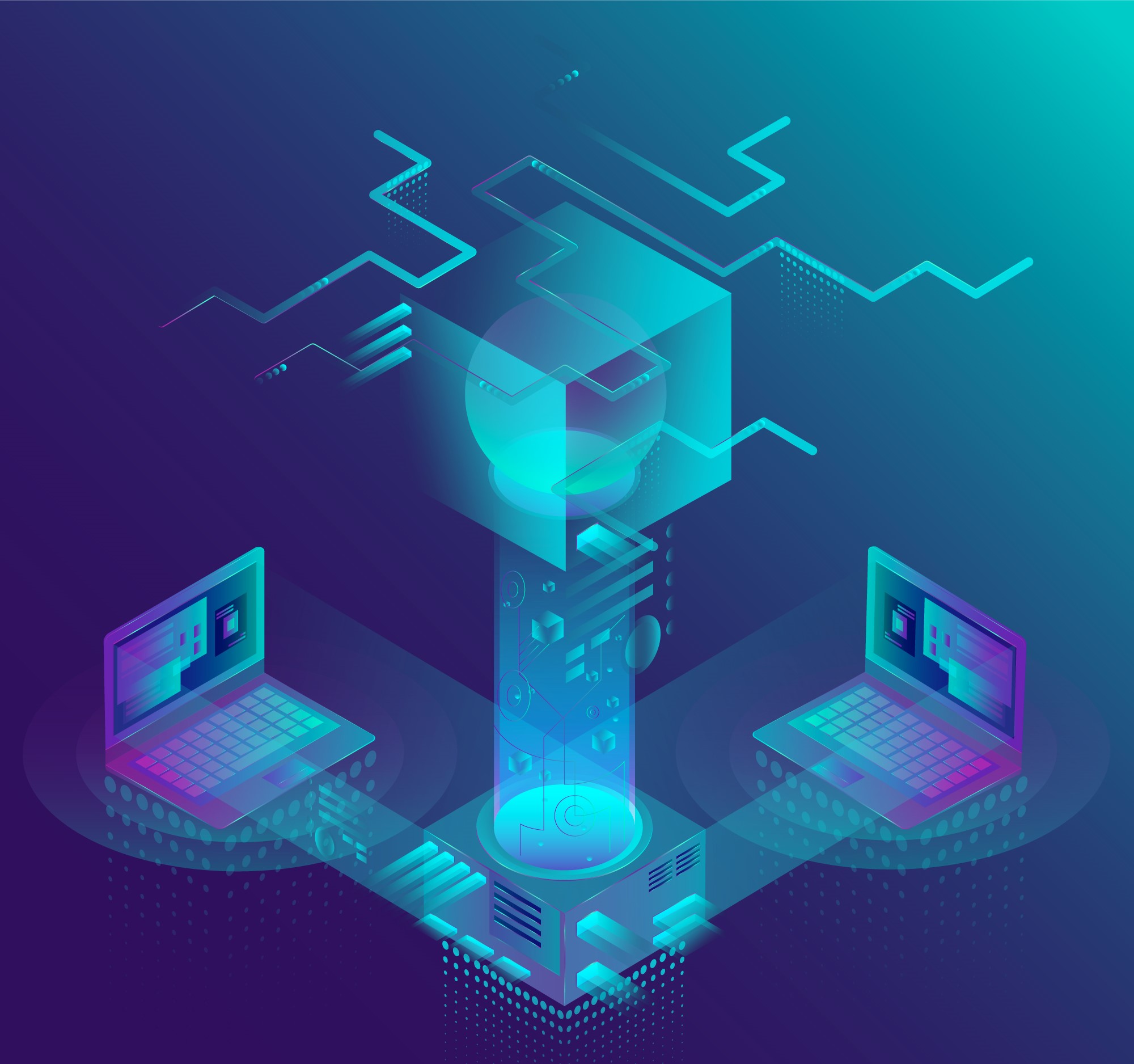