Fraunhofer ISIT develops energy-efficient and environmentally friendly manufacturing process for electrode foils in lithium-polymer batteries
Lithium-ion batteries have become an indispensable part of our everyday lives. They supply power to our cell phones and laptops, are installed as an energy source in electric vehicles and, as large stationary battery systems, provide the power supply and storage for many industrial applications. The manufacture of these battery cells is well established and involves many sequential process steps. Conventional solvent-based electrode production delivers very good results, but is characterized by high resource and energy consumption. Scientists at Fraunhofer ISIT are working on how production can be carried out more cost-effectively and in a more environmentally friendly manner, focusing on solvent-free production of the electrodes. After all, cost-effective and at the same time environmentally friendly production methods are a must for future battery cell production in order to serve the numerous fields of application.


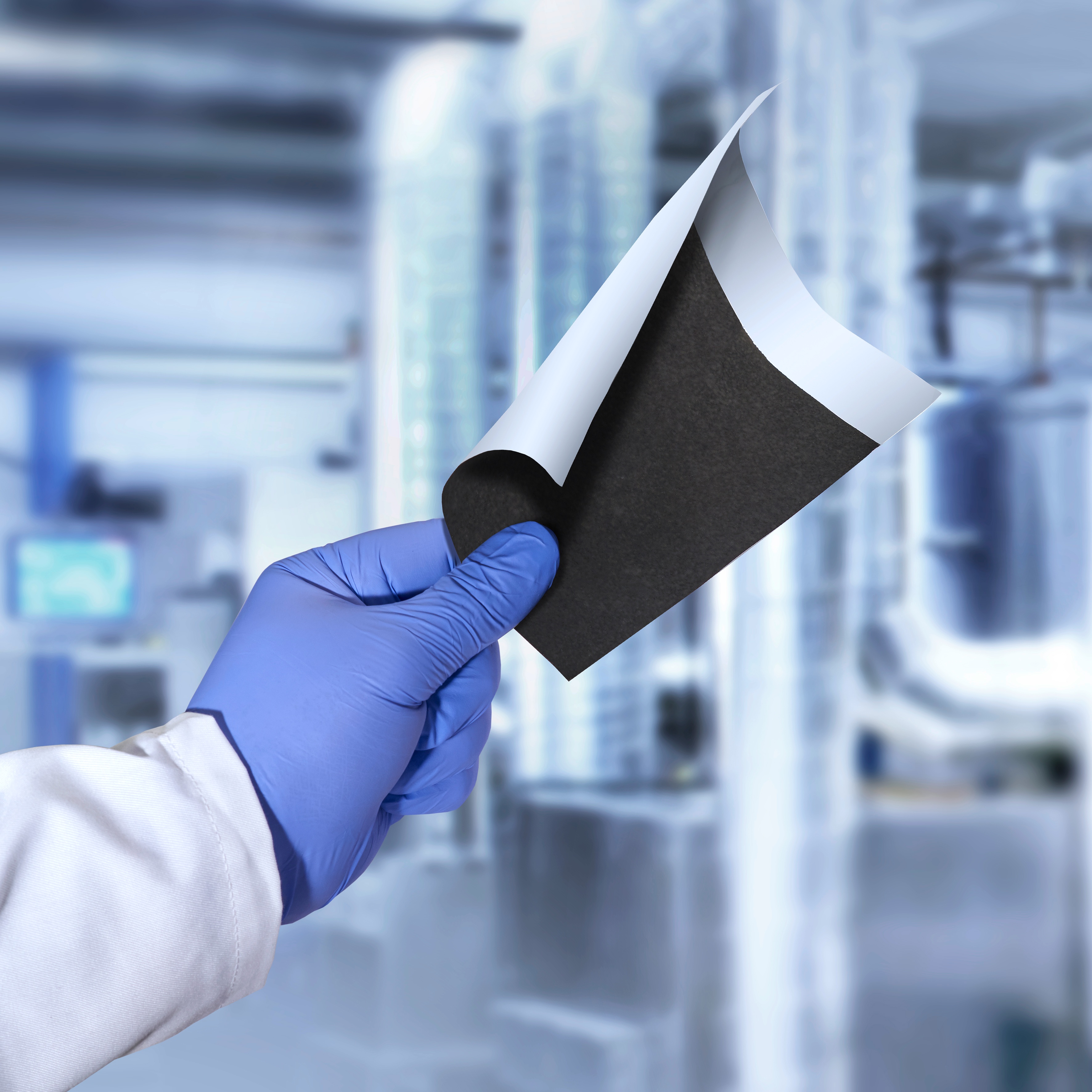
Normally, electrode foils are produced in larger quantities in a roll-to-roll process. In coating plants, the substrate material, which is on large rolls, is continuously unwound over a number of rollers and coated with the electrode material. In this process, a suspension of solvent, active material and a binder, which ensures the adhesion of the material, is applied to a metal foil. The coated electrode foil then passes through a drying oven and is finally rewound onto another roll. These lines are very large; they can be up to a hundred meters long, depending on the duration of the drying process.
This production method has several disadvantages: the production of the suspension takes a very long time, the solvent is harmful to the environment, and due to the long drying time in the oven, the process itself is very energy-intensive.
That's why the ISIT scientists are relying on a solvent-free dry coating process. They produced a powder mixture of active material, conductive additives and a suitable binder. In order to produce as uniform an application as possible and precisely defined layer thicknesses, this powder mixture is applied to the substrate using a special spreading process.
The amount of powder applied can be precisely adjusted by the spreading parameters and by the speed at which the carrier film passes through the machine. In principle, the scientists faced the same challenge as a confectioner who wants to spread powdered sugar on his cake as evenly as possible, without lumps. The material is then fixed to the carrier in a short temperature process.
The new solvent-free dry coating process patented by ISIT for the production of Li-ion battery electrodes is promising. With comparable electrochemical properties to electrodes from established production, this new process will not only enable significantly more compact production lines in the future, but also primary energy savings of up to 50%, since the long and energy-intensive drying sections during production are eliminated. Both the time savings in producing the powder mixture and the significantly reduced energy requirements for coating due to the elimination of drying offer optimum conditions for reducing resource and cost requirements.
"Dry coating technology has the potential to significantly reduce the costs and emissions of electrode production compared to the processes commonly used today. The process developed at ISIT thus makes a direct contribution to the development of economical and environmentally friendly storage technologies for mobile and stationary applications," summarizes the head of the project at Fraunhofer ISIT, Jannes Ophey.
Fraunhofer ISIT will present the new dry coating technology at Hannover Messe Energy 2022 at the Schleswig-Holstein joint booth,
Hall 13, Booth D 50.