With their enormous power density, laser beams can weld and cut steel plates, polish workpieces or build up entire engine blocks layer by layer from metal powder in 3D printing. Highly reflective layers make it possible to use micromirror scanners in MEMS technology for precise path control.
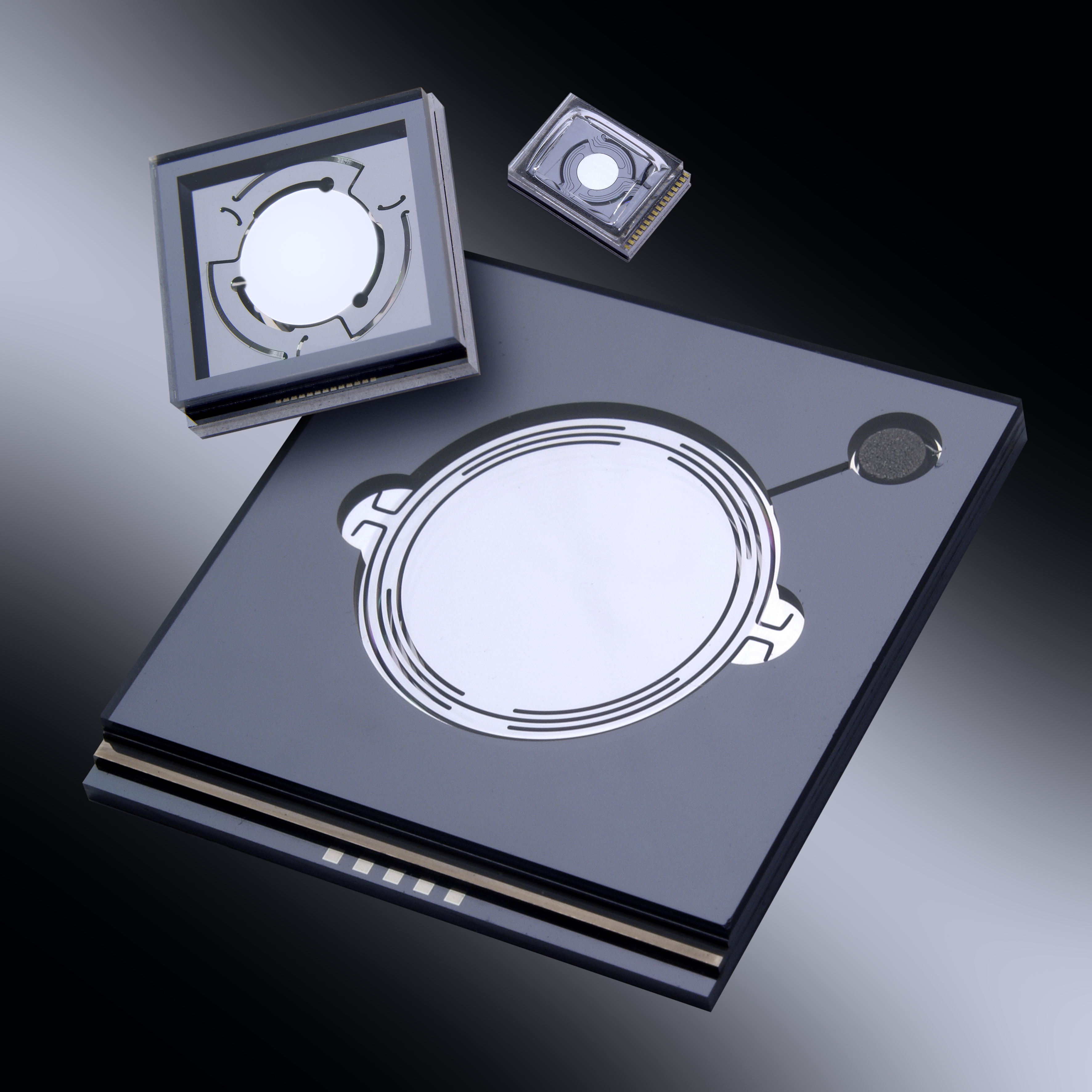
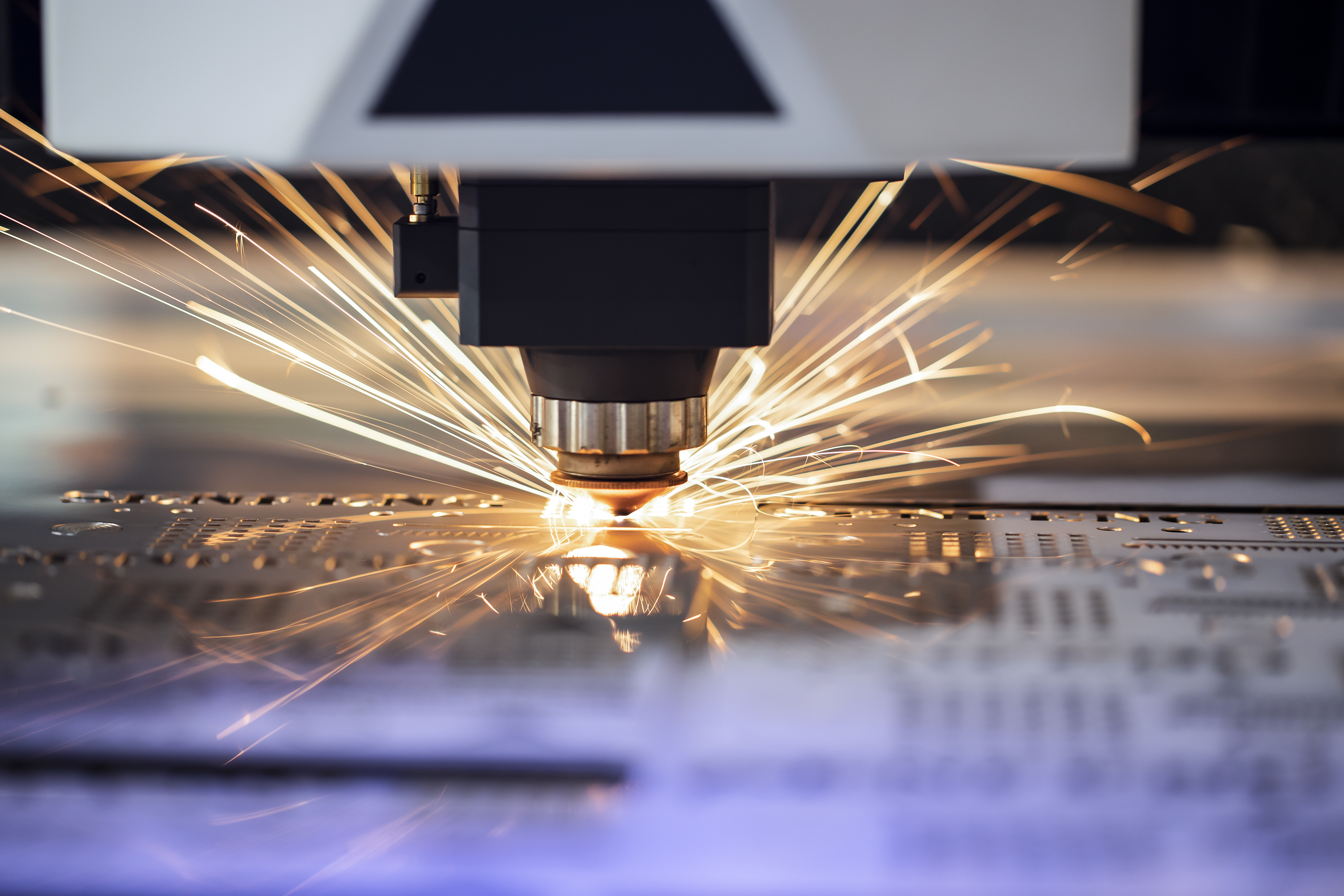
With its filigree drive structures, the micromirror scanner looks as if it would go up in smoke at the first laser pulse. But thanks to a multilayer optical coating system, over 99.9% of the irradiated laser power is reflected at a precisely defined light wavelength, enabling material processing by laser beam.
MEMS - Micro-Electro-Mechanical Systems - are manufactured like a microelectronic chip from a piece of silicon using semiconductor technology methods. However, silicon is used here as a mechanical material and not as a semiconductor: Thanks to their high elasticity, the crystalline structures can be processed into bending springs in micrometer dimensions. Photolithographic structuring and a variety of coating and etching processes are used to produce drive elements through which a mirror surface can be deflected in one or two directions. For example, piezoelectric layers ensure that a bending spring deflects as soon as an electrical voltage is applied. Even though the layer thicknesses are usually only thousandths of a millimeter, they can tilt a mirror by up to 45° to each side thousands of times per second by resonant oscillation, thus achieving an optical scan angle of 180°.
For material processing, the laser power is distributed over a large mirror area. The large optical aperture enables sharp focusing on the workpiece. Mirror surfaces up to 2 cm in diameter were developed in the LAMM (Large Aperture MEMS Scanning Mirrors) project and presented at LASER World of Photonics in 2015. Without a highly reflective coating, the absorbed heat could not be dissipated and the mirror would be destroyed immediately. To prevent this from happening, more than 99.9% of the light at the laser wavelength must be reflected. Thanks to their coatings, 8 mm mirrors withstood continuous wave lasers (1064 nm) of up to 600 W power, and even up to 2 kW depending on the design.
In the current CAPS project (Cluster of Excellence Advanced Photon Sources), the coating system for ultra-short pulse lasers (around 1030 nm) was optimized. Power levels averaging 340 W were successfully validated. At a repetition rate of 400 kHz and pulse durations of 2 ps with 1 mJ energy input each, damage occurred only from 1.75 J/cm² energy density. - The Fraunhofer research cluster CAPS aims at new key technologies for tomorrow's industry, such as higher laser power, new concepts for beam shaping and multi-beam processing of workpieces. By combining MEMS and galvanometer scanners, for example, a fast oscillation can be superposed with the machining trajectory to optimize the energy distribution.
Depending on the application, the MEMS scanners of Fraunhofer ISIT can have different mirror areas, can scan circularly or linearly, or can be designed as vector scanners for arbitrary trajectories. A customer-specific trade-off between aperture size, scan angle and speed must always be found. Fraunhofer ISIT manufactures the MEMS scanners in its own clean room and uses mechanical and optical simulation techniques to reliably predict the expected system properties and beam qualities. Highly reflective coating systems can be applied by other Fraunhofer institutes or by external service providers on request.
ISIT will present its micromirror scanners at LASER World of Photonics from June 27 to 30, 2023 in hall A2 at Fraunhofer booth 415.