Sven Grünzig, Matthias Landwehr and Sascha Bönhardt
Autonomous power supply for networked sensors
Fraunhofer researchers have set themselves the task of supplying networked sensors with sufficient energy and storing the energy locally. The result is a variety of novel components.

Fraunhofer researchers are working on the lead project "Towards Zero Power Electronics" to develop electronic and networked systems that require as little energy as possible. One of the results is a complete sensor system: the Smart City Sensor. It can be used to measure particulate matter in the city. Until now, it has been extremely costly to measure particulate matter in the air. In cities, therefore, measurement data can only be collected simultaneously at a selected few intersections. With their new development, the Fraunhofer researchers want to enable denser and more accurate measurement.
The energy-autonomous sensor nodes can be attached to street lamps or buses to determine particle concentrations in the ambient air. Intelligent networking of the nodes and connection to common cloud platforms creates a detailed model of particulate emissions in the city. There are virtually no limits to the applications: Traffic flow can be controlled via the networked sensors, or navigation systems orient themselves and adjust their routes independently. In many cases, the required energy is generated by solar cells. In tunnels, in pipes, under bridges or in street canyons, the energy source is no longer needed. The Fraunhofer researchers looked for alternative, suitable energy sources and developed new processes to use them to generate energy for the system. One idea, for example, was to couple the sensor system with a small, very smooth-running wind turbine that rotates even through the slightest air currents. Magnets mounted on the windmill vibrate an energy harvester integrated into the system. The energy harvester module converts the mechanical oscillations into electrical energy, stores it and then makes it available to the system in a precise manner.

A look at the micromechanical harvester.
The system requires the energy of the harvesting module primarily for the IoT core. This is a very energy-efficient computer unit that is also an interface to the outside world. The individual components of the harvesting module are a micromechanical harvester developed at Fraunhofer ISIT, which uses a novel manufacturing concept to enable magnetic excitation. Thanks to the use of modern materials, the harvester can generate a larger amount of electrical energy, which was previously reserved for much larger components. In addition, there is an integrated circuit to convert the energy from the harvester. This enables the harvesting module to significantly extend the battery life of each autonomous sensor node.
A first step to increase the power density was to develop scandium aluminum nitride layers and integrate them into the bending beam of the harvester. With the improved material, it is possible to increase the power by a factor of three compared to previous aluminum nitride-based harvesters. Another approach to increasing power density was to replace the silicon flywheel mass with higher density materials. This involves manually attaching a prefabricated magnet to the bending beam after the silicon manufacturing process - a complex and therefore expensive procedure.

More power thanks to a neodymium magnet
Fraunhofer ISIT has developed PowderMEMS technology, a process technology that makes it possible for the first time to directly integrate micrometer-sized NdFeB magnets into the semiconductor manufacturing process at wafer level. In addition, the process is compatible with all common process steps in microelectronics. Previously etched cavities in the substrate are filled with an NdFeB powder. Subsequently, a thin aluminum oxide layer is created around the individual particles via atomic layer deposition. The thin aluminum oxide layer bonds the individual particles and simultaneously protects them from environmental influences. Thanks to the stronger micromagnet, not only higher deflections in the spring-mass system, but also complex excitation possibilities of the harvester are possible at the same time. Rotational and translational movements are converted into energy by means of externally mounted magnets.
By moving the external magnet past the bending beam, it is strongly deflected. If the initial deflection is sufficiently strong and the magnetic field then abruptly decays, the bending beam oscillates at its resonant frequency. At low frequencies significantly below the resonance frequency, high energy yields are achievable, which is difficult to implement in conventional systems. Outputs of up to 80 µW at about 50 Hz and more than 150 µW when operating in resonance have been achieved with the harvester.
In addition, the Harvester can be used as a near-zero power wake-up receiver. After rectification, the voltage is sufficient to wake up an externally powered microcontroller. Accordingly, in standby mode, power consumption is low, hovering around a few picoamperes. Such a system allows to significantly increase the lifetime of electronic devices, which show longer standby times between their actual use.
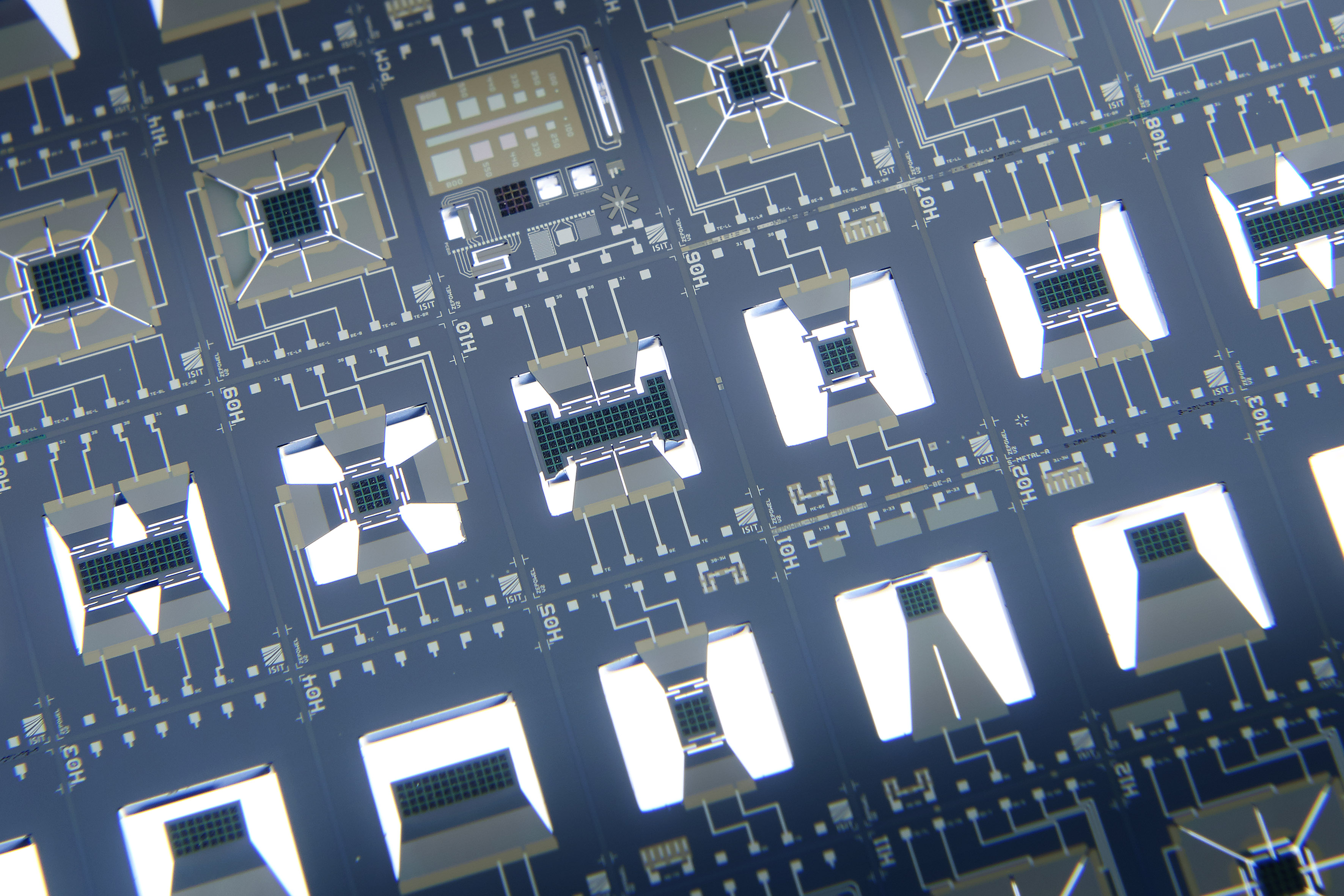
Converting the voltage efficiently with an ASIC
The AC voltage generated by the harvester is converted to a DC voltage by the energy converter ASIC, stepped up and the energy is then stored. The goal is optimized power matching together with the broadband input voltage and maximum circuit efficiency. The ASIC is based on two fully integrated converter concepts that enable highly efficient voltage conversion. Only transistors and capacitors are used for integration, with no transformers. The ASIC pad stages are powered by both an external voltage and the generated rectifier voltage. The design, with an area of 10 mm², was designed using a low-cost bi-polar/CMOS-on-SOI technology with 180 nm and fabricated via multi-project wafer run. In the block negative-half-wave converter of the NPCORE variant, the negative and positive envelopes are generated from the input voltages. The latter is applied to the input of the first stage of the following five-stage transistor rectifier.
An overall efficiency of 71 percent
To lower the effective threshold voltage, the bulk nodes of the MOSFET transistors are connected to the lowest or highest potential. The buffered output voltage of the last stage is fed to the output via Schottky diodes. The overall efficiency of the NPCORE version is 71%. Output powers of up to 70 µW are possible. The circuit concepts developed can be flexibly adapted to different harvester types, voltage ranges and output loads and enable energy conversion tailored to the specific application. A micro-energy storage system was developed so that the energy provided by the harvester can be stored.
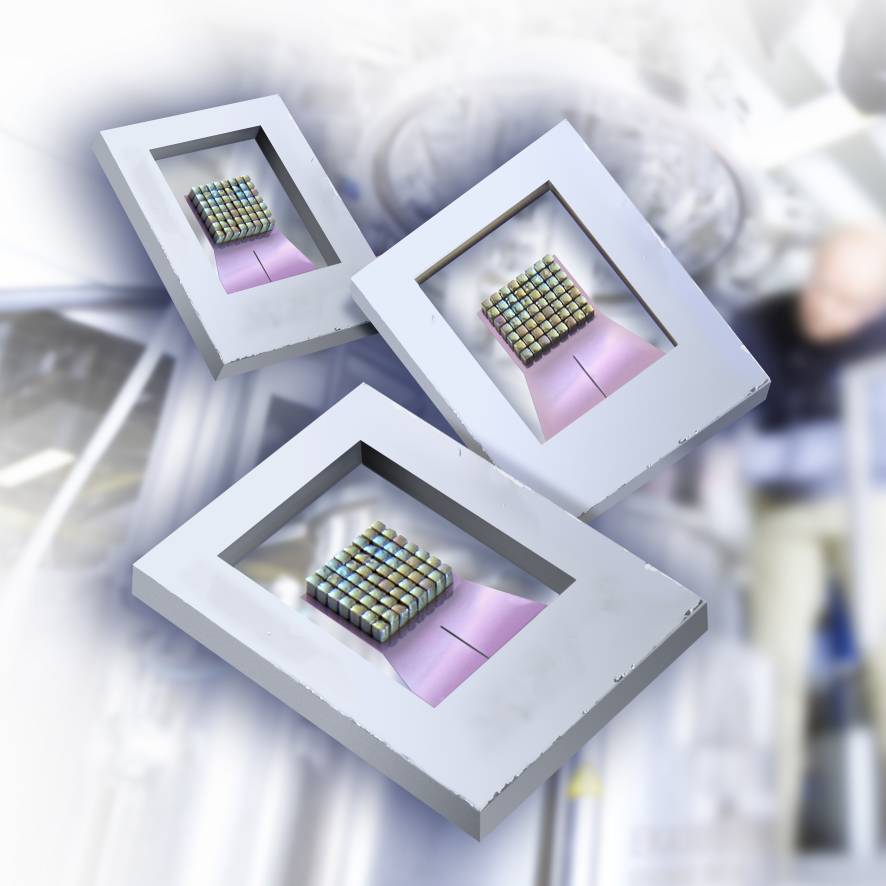
Homogeneous coating under extreme topologies
In addition to the dielectric layer, the lower and upper electrodes must be deposited into the structures with high precision. Atomic layer deposition is used here. This enables homogeneous coating of even extreme topologies. The capacitors produced have a thickness of 50 µm and a capacitance density of around 500 nF/mm². The use of anti-ferroelectric (AFE) dielectrics doubles the capacitance compared to conventional dielectrics. A capacitance of 800 nF/mm² was achieved. Around 4,000 components can be accommodated on a substrate (300 mm wafer) commonly used in microelectronics. The capacitors are then automatically separated and stored in vacuum release trays.